ironknocker
Neuling
Hi Leute,
ich starte dann mal mein neues Projekt.
Für das Projekt musste ich mir erst mal Werkzeug bestellen.
Als Material kommt Alu und Plexiglas zum Einsatz.
Das wird ein Case mit Gerippen von Flugzeugtragflächen dazu kommt dann die Wasserkühlung (hydro)
So was in der Richtung:
Hier mal ne erste Zeichnung.
Am freitag war der Postbote war da
Schlichthammer
Schweifhammer
Und Kugel Treibhämmer in verschiedenen Größen
Jetzt geht es mit dem Werkzeugbau los
Als erstes habe ich mir ein Treibkissen gebaut bzw genäht.
Dazu musste ne alte Stretch Jeans von Maria her halten.
Die habe ich dann erst mal zerlegt und zugeschnitten.
Dann habe ich alles vernäht, bis auf die Öffnung zum befüllen.
Normalerweise sind die Kissen mit Stahlkugeln gefüllt und aus leder.
Ich habe das Kissen mit feinem Vogelsand gefüllt.
Durch das Stretch Material lässt sich das super formen.
Dann der erste Test. Klappt wunderbar
Dann habe ich die Wölbung platt getrieben.
da könnte man jetzt einen Taster verdeckt montieren oder als Fuß benutzten.
Hier der Clip wie ich die Halbkugel mit dem Kissen gemacht habe.
An dieser Stelle möchten wir Ihnen ein Youtube-Video zeigen. Ihre Daten zu schützen, liegt uns aber am Herzen: Youtube setzt durch das Einbinden und Abspielen Cookies auf ihrem Rechner, mit welchen sie eventuell getracked werden können. Wenn Sie dies zulassen möchten, klicken Sie einfach auf den Play-Button. Das Video wird anschließend geladen und danach abgespielt.
Youtube Videos ab jetzt direkt anzeigen
Dann habe ich heute mal Versuche mit Löchern und Kanten gemacht.
Dazu habe ich mir aus Rohren und einem Stück Flachstahl eine Schablone gemacht.
Als nächstes habe ich dann ein Loch in ein 1mm Loch gebohrt. Das Blech habe ich dann über die Schablone gelegt.
Wichtig dabei ist das man das Blech genau mittig ausrichtet, damit man eine Gleichmäßig hohe Kante bekommt.
Jetzt kann gedängelt werden.
So schaut das von der anderen Seite aus.
Mit dem Schweifhammer habe ich noch eine Außenkante um eine Rundung gekantet.
Zulestz habe ich dann noch eine gerate Kantung ins Blech gemacht und fertig ist mein Probestück
ich starte dann mal mein neues Projekt.
Für das Projekt musste ich mir erst mal Werkzeug bestellen.
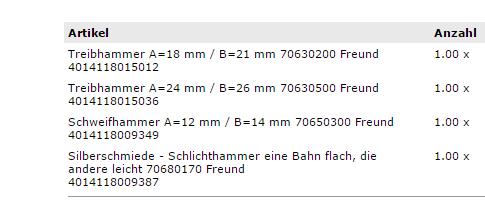
Als Material kommt Alu und Plexiglas zum Einsatz.
Das wird ein Case mit Gerippen von Flugzeugtragflächen dazu kommt dann die Wasserkühlung (hydro)
So was in der Richtung:


Hier mal ne erste Zeichnung.
Am freitag war der Postbote war da
Schlichthammer
Schweifhammer
Und Kugel Treibhämmer in verschiedenen Größen
Jetzt geht es mit dem Werkzeugbau los
Als erstes habe ich mir ein Treibkissen gebaut bzw genäht.
Dazu musste ne alte Stretch Jeans von Maria her halten.
Die habe ich dann erst mal zerlegt und zugeschnitten.
Dann habe ich alles vernäht, bis auf die Öffnung zum befüllen.
Normalerweise sind die Kissen mit Stahlkugeln gefüllt und aus leder.
Ich habe das Kissen mit feinem Vogelsand gefüllt.
Durch das Stretch Material lässt sich das super formen.
Dann der erste Test. Klappt wunderbar
Dann habe ich die Wölbung platt getrieben.
da könnte man jetzt einen Taster verdeckt montieren oder als Fuß benutzten.
Hier der Clip wie ich die Halbkugel mit dem Kissen gemacht habe.
Datenschutzhinweis für Youtube
An dieser Stelle möchten wir Ihnen ein Youtube-Video zeigen. Ihre Daten zu schützen, liegt uns aber am Herzen: Youtube setzt durch das Einbinden und Abspielen Cookies auf ihrem Rechner, mit welchen sie eventuell getracked werden können. Wenn Sie dies zulassen möchten, klicken Sie einfach auf den Play-Button. Das Video wird anschließend geladen und danach abgespielt.
Youtube Videos ab jetzt direkt anzeigen
Dann habe ich heute mal Versuche mit Löchern und Kanten gemacht.
Dazu habe ich mir aus Rohren und einem Stück Flachstahl eine Schablone gemacht.
Als nächstes habe ich dann ein Loch in ein 1mm Loch gebohrt. Das Blech habe ich dann über die Schablone gelegt.
Wichtig dabei ist das man das Blech genau mittig ausrichtet, damit man eine Gleichmäßig hohe Kante bekommt.
Jetzt kann gedängelt werden.
So schaut das von der anderen Seite aus.
Mit dem Schweifhammer habe ich noch eine Außenkante um eine Rundung gekantet.
Zulestz habe ich dann noch eine gerate Kantung ins Blech gemacht und fertig ist mein Probestück