@patrock84
Ich wäre durchaus dazu in der Lage gewesen die Backplate von Hand "auszuschnitzen"🔨💪 Aber egal wie viel Mühe ich mir gegeben hätte, ich hätte es nicht in 34 Sekunden geschafft.🤣
Der handwerkliche Part war in diesem Fall Tatsache das Schweißen,Richten und Schleifen. All diese Arbeiten wurden von mir komplett händisch ausgeführt und sind bei 1mm dickem Blech auch nicht ganz ohne.
@citsejam
Die Erklärung von patrock84 ist, bis auf eine Kleinigkeit, völlig korrekt. Der Brennpunkt (Fokus) ist beim Laserschneiden ein sehr wichtiger Faktor. Er liegt je nach zu bearbeitendem Material, verwendeter Schneid Technologie/Strategie, mal über dem Material und mal im Material, seltener darunter. Nach dem verlassen dieses Punktes verliert der Laserstrahl immer mehr Energie da er quasi zerstreut wird, also nicht mehr so stark gebündelt ist und auch schon viel der Energie in Wärme(Schneidprozess) umgewandelt wurde. Der Strahl ist dann aber immer noch so energiereich das er nach und nach tatsächlich seine Auflagestege (Arbeitsplatte) zerschneidet. Diese müssen also regelmäßig ersetzt werden, was je nach verwendetem Material (Stahl\Edelstahl\Kupfer) und Menge der Auflagestege zwischen ein paar hundert und ein paar tausend Euro kosten kann. Das war jetzt alles stark vereinfacht dargestellt, sollte aber ausreichen um einen kleinen Einblick zu ermöglichen.
@foxxx
Der Laser aus dem Video ist eher ein "Einsteigermodell". Out of the Box schneidet er zB. 15mm Stahl DD11 bis zu einer max. Größe von 3000x1500 mm mit einer Genauigkeit von +/- 0,1mm.
Wenn man sich Mühe gibt und die "Schneidparameter" anpasst auch +/- 0,05mm. Dabei entsteht an der Schnittkante eine Rz von ca. 50-100. Was in der Zerspanungswelt, wenn ich mich recht entsinne, ungefähr einer geschruppten Oberfläche entsprechen sollte. Gratbildung gibt es, wenn der Schneidprozess optimal läuft und das Material nicht totaler Schrott ist, auch nicht.
Die Schnittkantenqualität ist auch sehr stark abhängig von der benutzten Strahlenquelle(Co2 / Festkörperlaser) und zb. der daraus resultierenden unterschiedlichen Wellenlänge.
Kann deine Aussage "ab 5mm+ unsauber und Ausriss", zumindest meiner Erfahrung nach nicht bestätigen. Wenn es natürlich um die letzten 0,01/0,001 mm, Passungen,präzise Bearbeitung großer Querschnitte oder "feinste" Oberflächen geht, kommt man natürlich an einer CNC Fräse oder Drehmaschine nicht vorbei.
Jetzt aber mal zum eigentlichen Thema
Die Fittinge und Tubes sind endlich da.

EKWB habe ich zuvor noch nie benutzt. Bin also auf Qualität und Passgenauigkeit gespannt. Hab ein wenig quer Beet bestellt.
Tubes sind 16/12 er Acrylrohre. Da ich bisher immer Schlauchverleger war, hab ich mir mal so einen Eiskoffer, zur Unterstützung des Biegeprozesses, bestellt. Auch bei diesem bin ich auf Qualität und Handhabung gespannt. Vllt. unternehme ich am We meine ersten Biegeversuche.
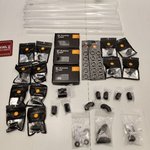
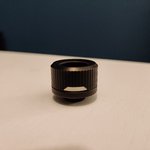
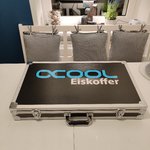
Und noch ein paar Kleinigkeiten von AC. Für die ganzen Splitty´s muss ich mir auch noch irgendwie ne sinnvolle Halterung ausdenken

.
Mein Plan/Traum ist es mit dieser Gerätekombination alle 6 Corsair QL 120, PWM DDC, RGB der Distro, RGB des CPU-Kühlers und RGB des Gehäuses über die AquaSuite steueren zu können.
Hat jemand von euch schon Erfahrung mit Corsair Lüftern + AquaSuite?
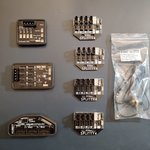
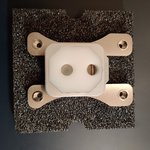
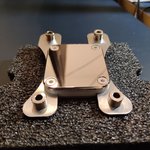
Wünsche allen ein schönes We🏝