Quantor
Enthusiast
Hallo Luxx-Community,
der ein oder andere erinnert sich vielleicht noch: Vor einiger Zeit hatte ich hier im Forum schon einmal ein "Großprojekt" am Start. Das Projekt lief damals unter dem Namen "Heaven & Hell" und dabei handelte es sich (auch) um einen Schreibtisch mit zwei eingebauten PCs.
Hier erst einmal der Link zu meinem alten Worklog für die, die es eventuell interessiert:
Heaven & Hell DeskCon Project
Anfangen möchte ich aber auch diesmal mit einer Vorstellung meines Projektes:
Gründe für einen Neubau:
Mein "Heaven & Hell" Schreibtisch ist jetzt bereits seit über drei Jahren im "Einsatz" und hat sich bis heute auch in jeder Hinsicht bewährt (alles funktioniert noch wie am ersten Tag). Seit der Fertigstellung hat sich aber so einiges geändert und daher wird es Zeit einen Neubau in Angriff zu nehmen. Dafür gibt es mehrere Gründe:
Wie Ihr also sehen könnt: Genug Gründe um einen Neubau in Angriff zu nehmen.
Das neue Konzept:
Das Projekt habe ich diesmal "Good & Evil" getauft. "Heaven & Hell 2.0" fand ich doof, da es ein komplett neues Design mit neuen Herausforderungen sein wird. Mit der neuen Namensgebung möchte ich allerdings zum einen einen thematischen Bezug zum Vorgängerprojekt herstellen, zum anderen aber auch ein bissel Wortspielerei betreiben.
Diejenigen, die mein altes Projekt verfolgt haben kennen bestimmt noch mein Faible für Ambigramme, also Schriftzüge die auf dem Kopf stehend die selben Worte ergeben, bzw. andere Worte erscheinen lassen. Bekannt sind diese typographischen Elemente vor allem durch den Dan Brown Roman "Illuminati" und dessen Verfilmung geworden. Bei meinem letzten Projekt konnten die Schriftzüge für Heaven / Hell jeweils um 180 Grad gedreht werden und ergaben die gleichen Wörter.
Auch diesmal habe ich deshalb wieder ein Ambigramm als Projektlogo gewählt. Während damals "Heaven" für meinen Arbeits-PC und "Hell" für meinen Gaming-PC standen ist die Bedeutung diesmal eine andere: Ich gehöre keinem speziellen Fanboy-Lager an. Ich mag Intel-Prozessoren genauso sehr wie AMD-Prozessoren. Ich habe sowohl Geforce als auch Radeon-Grafikkarten. Ich nutze sowohl iOS (Apple)-Geräte, als auch Android-Devices. In unserem Haushalt gibt es sowohl eine PS4, als auch eine XBox One, usw. All dies bedeutet aber nicht, dass ich mich mit der ein oder anderen Firmenphilosophie identifiziere oder diese für Gut befinde. Ganz im Gegenteil, es gibt durchaus Dinge an Unternehmen wie Apple, Intel, AMD oder NVIDIA die ich absolut nicht leiden kann. Dies ändert aber nichts daran, dass all deren Produkte eine Daseinsberechtigung haben und von mir auch genutzt werden.
Daher steht das "Good & Evil" Logo diesmal für beide PCs gleichzeitig. Und je nachdem welche Seite der ein oder andere Leser vielleicht präferiert kann er sich das Logo so drehen, wie er es will
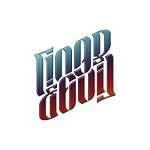
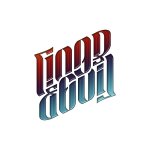
Wie das Logo schon erahnen lässt, wird der Schreibtisch jeweils ein Intel- und ein AMD-System beherbergen. Auch werden wohl sowohl eine Radeon, als auch eine Geforce Grafikkarte zum Einsatz kommen. Sollte also für jeden etwas dabei sein.
Wie schon beim letzten Mal wird sich wohl der ein oder andere fragen, warum überhaupt zwei PCs in den Tisch rein sollen. Und die Antwort ist auch diesmal wieder die gleiche: Ein PC ist hauptsächlich zum spielen gedacht und der andere für Arbeit/grafische Anwendungen. Ich arbeite z.B. sehr gerne und viel mit Blender. Und während der eine Rechner rendert, kann ich auf dem zweiten immer noch spielen. Bei längeren Animationen sind auch zwei Rechner, die gleichzeitig ein Projekt rendern, nicht die schlechteste Idee.
Auch diesmal will ich nicht irgendeine "Kopie" eines vorhandenen Projektes bauen, sondern natürlich auch wieder ein paar Dinge integrieren, die man bisher nur selten gesehen hat, bzw. die vielleicht noch keiner auf diese Art und Weise verwirklicht hat. Andere Elemente, die sich in der Vergangenheit (für mich) bewährt haben, möchte ich aber in abgewandelter Form aus meinem alten Projekt übernehmen.
Bevor ich das Projekt jetzt aber offiziell enthülle hier noch "schnell" die geplante Featuresliste:
Das Design:
Stellt sich natürlich noch die Frage, wie der neue Tisch denn nun aussehen soll. Wie auch schon in der Vergangenheit habe ich das neue Projekt mit SketchUp grob entworfen und dann mit Raylectron und Blender entsprechend gerendert. Beim Bau werde ich mich auch diesmal weitestgehend an meinen Entwürfen orientieren. Es gibt aber auch noch Bereiche, die sich während der Umsetzung noch ändern können/werden.
Doch jetzt erst einmal genug geschwafelt: Hier präsentiere ich mein Vorabentwürfe, die ich dann bei Bedarf noch anpassen werde:
Materialien:
Im Gegensatz zum vorherigen Projekt werde ich diesmal mit MDF-Platten als Hauptbaumaterial arbeiten. MDF ist wesentlich stabiler und "steifer" als die beim letzten mal verwendeten Möbelbauplatten. Dies ist gerade für den ausfahrbaren Korpus sehr wichtig. Allerdings kommt mit den MDF-Platten auch ein höheres Gewicht daher, was dem Hebemechanismus hoffentlich nicht zu sehr zu schaffen machen wird. Hinzu kommen dann noch Plexiglas und echtes Glas und das ein oder andere Teil aus dem 3D-Drucker.
Sponsoring:
Diejenigen unter Euch, die schon mein letztes Projekt verfolgt haben können sich vielleicht daran erinnern, dass ich das "Heaven & Hell" Projekt damals ohne einen Sponsor und Unterstützung begonnen hatte. Nachdem damals aber ein Unternehmen hier im Forum auf das Projekt aufmerksam wurde und mir ein wenig Unterstützung zur Seite stellte. Im Laufe des Projektes kamen dann noch ein paar hinzu und haben es mir ermöglicht mein Budget auf den eigentlichen Bau zu verwenden.
Auch bei diesem Projekt werde ich meinen selbst gesetzten Kostenrahmen locker und schneller sprengen als mir lieb sein dürfte, daher habe ich mich diesmal dazu entschieden schon im Vorfeld nach entsprechender Unterstützung zu suchen und bin auch entsprechend fündig geworden.
Daher möchte ich mich schon jetzt bei den folgenden Unternehmen für ihre Unterstützung und den Support meines Projektes bedanken: (in alphabetischer Reihenfolge)
Alphacool
Für die Versorgung mit Kühlkomponenten und Zubehör.
Cooler Master
Für Lüfter, Netzteil, Tastatur, Maus, Mauspad
Flatlift TV Liftsysteme GmbH
Für das zur Verfügung stellen eines geeigneten Hebesystems für den ausfahrbaren Korpus
MSI Deutschland
Für die Versorgung mit entsprechenden Systemkomponenten
XPG/AData
Für die Grundausstattung mit RAM-Kits und SSDs.
Tausend Dank dafür !!!
Farbgebung:
Ich habe mich noch nicht endgültig auf eine Farbe für den Tisch festgelegt. Mit dem entsprechenden Arbeitsaufwand lassen sich die MDF-Platten aber in jeder Farbe lackieren. Auch bin ich mir noch nicht schlüssig ob der Tisch am Ende ein Hochglanz- oder ein mattes Finish erhalten wird. Eventuell wird das Projekt auch mehrfarbig (Hauptfarbe / Akzentfarbe).
Um mal einen Eindruck vom möglichen Endergebnis zu bekommen, habe ich mal ein wenig mit den virtuellen Farbeimern von Blender rumgespielt. Hier die Ergebnisse:
Mal schauen was es dann im Endeffekt werden wird....
Der Anfang:
Anfangen werde ich morgen mit dem zusägen der MDF-Platten und dann in den folgenden Tagen mit dem hinteren Teil des Korpus und mit dem ausfahrbaren Bereich.
Meine Erwartungen an diesen Thread und die Community:
Bei dem letzten Tisch-Projekt hat mich am meisten der Support und der Input aus der Community gefreut. Das ein oder andere von Euren Ideen hat es ja dann schließlich auch mit in das Projekt geschafft. Von daher würde ich mich auch diesmal über jede Menge "konstruktiven" Input und entsprechende Hilfestellungen bei eventuell auftauchenden Problemen freuen. Vielleicht verirrt sich ja auch der ein oder andere Abonnent vom letzten Projekt hierher...
Auch erhoffe ich mir ähnlich viel Spaß bei der Umsetzung wie beim letzten mal und vielleicht entstehen ja auch wieder neue Forenfreundschaften (von der es manche beim letzten Mal auch ins Real-Life geschafft haben).
Ich hoffe Ihr habt an diesem Worklog ähnlich viel Spaß, wie auch ich ihn haben werde.
So, zum Abschluss habe ich auch schon wie beim letzten mal ein Rendervideo erstellt, dass den grundsätzlichen Projektaufbau im Detail zeigt. Auf dem gleichen YT-Kanal werde ich nach Möglichkeit von Zeit zu Zeit das ein oder andere Video einstellen um bestimmte Details näher zu beleuchten.
An dieser Stelle möchten wir Ihnen ein Youtube-Video zeigen. Ihre Daten zu schützen, liegt uns aber am Herzen: Youtube setzt durch das Einbinden und Abspielen Cookies auf ihrem Rechner, mit welchen sie eventuell getracked werden können. Wenn Sie dies zulassen möchten, klicken Sie einfach auf den Play-Button. Das Video wird anschließend geladen und danach abgespielt.
Youtube Videos ab jetzt direkt anzeigen
Und nun wünsche ich Euch und mir viel Spaß mit meinem "Good & Evil" Projekt.
Viele Grüße,
Olli, aka Quantor
der ein oder andere erinnert sich vielleicht noch: Vor einiger Zeit hatte ich hier im Forum schon einmal ein "Großprojekt" am Start. Das Projekt lief damals unter dem Namen "Heaven & Hell" und dabei handelte es sich (auch) um einen Schreibtisch mit zwei eingebauten PCs.
Hier erst einmal der Link zu meinem alten Worklog für die, die es eventuell interessiert:
Heaven & Hell DeskCon Project
Anfangen möchte ich aber auch diesmal mit einer Vorstellung meines Projektes:
Gründe für einen Neubau:
Mein "Heaven & Hell" Schreibtisch ist jetzt bereits seit über drei Jahren im "Einsatz" und hat sich bis heute auch in jeder Hinsicht bewährt (alles funktioniert noch wie am ersten Tag). Seit der Fertigstellung hat sich aber so einiges geändert und daher wird es Zeit einen Neubau in Angriff zu nehmen. Dafür gibt es mehrere Gründe:
1. Damals hatte ich noch zwei 20" Monitore und einen 22" Monitor im Einsatz. Mittlerweile bin ich aber bei zwei 24" und einem 28" Monitor angelangt. Diese Monitore benötigen natürlich auch wesentlich mehr Platz auf dem Tisch, so dass die Breite der Stellfläche zwar gerade noch so ausreicht, allerdings keine Luft nach oben mehr ist. Auch ragen die äußeren Monitor über den Tisch hinaus und bergen die Gefahr, dass man aus Versehen dran hängen bleiben könnte.
2. Damals hatte ich zwei Wassersprudelsäulen gleichzeitig als Balancer und vordere Tischbeine in die Kühlkreisläufe mit eingebunden. Diese sind auch bis heute noch extrem stabil, allerdings machen die ein verrücken des Tisches (z.B. für Renovierungsarbeiten im Wohnzimmer) nahezu unmöglich. Zumindest nicht ohne Entleerung der Kühlkreisläufe und demontage der Säulen.
3. Ein "kleiner" Designfehler hatte sich in das alte Projekt eingeschlichen. Ich habe damals Hardtubes durch Kanäle in der hinteren Tischplatte verlegt und diese beleuchtet. Das sieht zwar richtig gut aus, allerdings hatte ich eins nicht bedacht: Diese hintere Platte ist auch gleichzeitig die Abdeckung vom "Technikkasten". Ich hatte zwar ausfahrbare USB-Hubs in die Platte eingelassen, allerdings nur welche für USB 2.0, was damals noch der Standard war. Wenn ich jetzt allerdings ein USB 3.0 Gerät an mein Motherboard anschließen will, dann muss ich auch hier beide Systeme komplett entwässern, um die hintere Platte öffnen zu können und Zugang zu den hinteren Anschlüssen des Motherboard zu erhalten. Das gleiche gilt natürlich auch nach dem wechseln einer Grafikkarte, usw.
4. Das Projekt war damals pass-genau auf meine damalige Hardware ausgerichtet. Mittlerweile habe ich aber bei einem System die Grafikkarte geupgraded, die dummerweise mit Fittings "höher" als die vorherige ist. Dadurch hat die Tischplatte nicht mehr auf den Korpus gepasst und ich musste diese künstlich mit Abstandshaltern aus dem 3D-Drucker erhöhen
5. Nach vielen kleineren Projekten, hauptsächlich im Bekanntenkreis, habe ich mal wieder so richtig Lust auf ein solches Großprojekt und den damit verbundenen Bastelspass
6. Bei dem alten Projekt hatte ich zwei kleine Touchscreens zur Anzeige von Systemdaten und Informationen vorne in die Front "eingelassen". Auch wenn diese tadellos funktionieren ist der Blickwinkel auf diese wenn man am Schreibtisch sitzt doch sehr ungünstig.
2. Damals hatte ich zwei Wassersprudelsäulen gleichzeitig als Balancer und vordere Tischbeine in die Kühlkreisläufe mit eingebunden. Diese sind auch bis heute noch extrem stabil, allerdings machen die ein verrücken des Tisches (z.B. für Renovierungsarbeiten im Wohnzimmer) nahezu unmöglich. Zumindest nicht ohne Entleerung der Kühlkreisläufe und demontage der Säulen.
3. Ein "kleiner" Designfehler hatte sich in das alte Projekt eingeschlichen. Ich habe damals Hardtubes durch Kanäle in der hinteren Tischplatte verlegt und diese beleuchtet. Das sieht zwar richtig gut aus, allerdings hatte ich eins nicht bedacht: Diese hintere Platte ist auch gleichzeitig die Abdeckung vom "Technikkasten". Ich hatte zwar ausfahrbare USB-Hubs in die Platte eingelassen, allerdings nur welche für USB 2.0, was damals noch der Standard war. Wenn ich jetzt allerdings ein USB 3.0 Gerät an mein Motherboard anschließen will, dann muss ich auch hier beide Systeme komplett entwässern, um die hintere Platte öffnen zu können und Zugang zu den hinteren Anschlüssen des Motherboard zu erhalten. Das gleiche gilt natürlich auch nach dem wechseln einer Grafikkarte, usw.
4. Das Projekt war damals pass-genau auf meine damalige Hardware ausgerichtet. Mittlerweile habe ich aber bei einem System die Grafikkarte geupgraded, die dummerweise mit Fittings "höher" als die vorherige ist. Dadurch hat die Tischplatte nicht mehr auf den Korpus gepasst und ich musste diese künstlich mit Abstandshaltern aus dem 3D-Drucker erhöhen
5. Nach vielen kleineren Projekten, hauptsächlich im Bekanntenkreis, habe ich mal wieder so richtig Lust auf ein solches Großprojekt und den damit verbundenen Bastelspass
6. Bei dem alten Projekt hatte ich zwei kleine Touchscreens zur Anzeige von Systemdaten und Informationen vorne in die Front "eingelassen". Auch wenn diese tadellos funktionieren ist der Blickwinkel auf diese wenn man am Schreibtisch sitzt doch sehr ungünstig.
Wie Ihr also sehen könnt: Genug Gründe um einen Neubau in Angriff zu nehmen.
Das neue Konzept:
Das Projekt habe ich diesmal "Good & Evil" getauft. "Heaven & Hell 2.0" fand ich doof, da es ein komplett neues Design mit neuen Herausforderungen sein wird. Mit der neuen Namensgebung möchte ich allerdings zum einen einen thematischen Bezug zum Vorgängerprojekt herstellen, zum anderen aber auch ein bissel Wortspielerei betreiben.
Diejenigen, die mein altes Projekt verfolgt haben kennen bestimmt noch mein Faible für Ambigramme, also Schriftzüge die auf dem Kopf stehend die selben Worte ergeben, bzw. andere Worte erscheinen lassen. Bekannt sind diese typographischen Elemente vor allem durch den Dan Brown Roman "Illuminati" und dessen Verfilmung geworden. Bei meinem letzten Projekt konnten die Schriftzüge für Heaven / Hell jeweils um 180 Grad gedreht werden und ergaben die gleichen Wörter.
Auch diesmal habe ich deshalb wieder ein Ambigramm als Projektlogo gewählt. Während damals "Heaven" für meinen Arbeits-PC und "Hell" für meinen Gaming-PC standen ist die Bedeutung diesmal eine andere: Ich gehöre keinem speziellen Fanboy-Lager an. Ich mag Intel-Prozessoren genauso sehr wie AMD-Prozessoren. Ich habe sowohl Geforce als auch Radeon-Grafikkarten. Ich nutze sowohl iOS (Apple)-Geräte, als auch Android-Devices. In unserem Haushalt gibt es sowohl eine PS4, als auch eine XBox One, usw. All dies bedeutet aber nicht, dass ich mich mit der ein oder anderen Firmenphilosophie identifiziere oder diese für Gut befinde. Ganz im Gegenteil, es gibt durchaus Dinge an Unternehmen wie Apple, Intel, AMD oder NVIDIA die ich absolut nicht leiden kann. Dies ändert aber nichts daran, dass all deren Produkte eine Daseinsberechtigung haben und von mir auch genutzt werden.
Daher steht das "Good & Evil" Logo diesmal für beide PCs gleichzeitig. Und je nachdem welche Seite der ein oder andere Leser vielleicht präferiert kann er sich das Logo so drehen, wie er es will
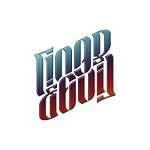
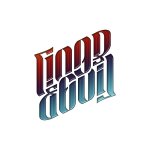
Wie das Logo schon erahnen lässt, wird der Schreibtisch jeweils ein Intel- und ein AMD-System beherbergen. Auch werden wohl sowohl eine Radeon, als auch eine Geforce Grafikkarte zum Einsatz kommen. Sollte also für jeden etwas dabei sein.
Wie schon beim letzten Mal wird sich wohl der ein oder andere fragen, warum überhaupt zwei PCs in den Tisch rein sollen. Und die Antwort ist auch diesmal wieder die gleiche: Ein PC ist hauptsächlich zum spielen gedacht und der andere für Arbeit/grafische Anwendungen. Ich arbeite z.B. sehr gerne und viel mit Blender. Und während der eine Rechner rendert, kann ich auf dem zweiten immer noch spielen. Bei längeren Animationen sind auch zwei Rechner, die gleichzeitig ein Projekt rendern, nicht die schlechteste Idee.
Auch diesmal will ich nicht irgendeine "Kopie" eines vorhandenen Projektes bauen, sondern natürlich auch wieder ein paar Dinge integrieren, die man bisher nur selten gesehen hat, bzw. die vielleicht noch keiner auf diese Art und Weise verwirklicht hat. Andere Elemente, die sich in der Vergangenheit (für mich) bewährt haben, möchte ich aber in abgewandelter Form aus meinem alten Projekt übernehmen.
Bevor ich das Projekt jetzt aber offiziell enthülle hier noch "schnell" die geplante Featuresliste:
1. In den Kühlkreislauf integrierte Wassersprudelsäulen als Balancer (und Blickfang). Allerdings diesmal nicht als Tischbeine. Diese werde ich aus meinem vorigen Projekt übernehmen, da sie sich bewährt haben. Meine Wassertemperaturen im Kreislauf sind bei meinem alten Tisch durchschnittlich um 1-2 Grad geringer wenn die Säulen eingeschaltet sind. Die "Frischluft" aus den Wassersäulen helfen durchaus mit die Kühlflüssigkeit im Kreislauf schneller wieder zu kühlen.
2. Zwei in den Korpus eingelassene Touchscreens, zur Anzeige von Systemdaten und zur Steuerung diverser Systemfunktionen. Diese übernehme ich ebenfalls aus dem Vorgängerprojekt. Allerdings werden sie diesmal wesentlich zugänglicher und sinnvoller verbaut.
3. Zusammenhängend mit den Touchscreens plane ich die Integration von einem oder zwei Raspberry-Pi's um über diese Sensordaten auszulesen, die Beleuchtung zu steuern und falls möglich noch ein paar andere Funktionen. Da ich mich allerdings noch nie so intensiv mit dem Pi beschäftigt habe, werde ich mich in die Thematik noch ein wenig herein arbeiten müssen.
4. Die Monitore werden in einem Korpus sitzen, der sich ein- und ausfahren lässt.
5. Der Haupt-Spiel-Monitor wird ein selbstgebautes Ambilight-ähnliches System zur Umgebungsbeleuchtung erhalten um die Immersion bei Spielen zu verstärken.
6. Das Projekt wird im Vergleich zu meinem alten Tisch recht "sportliche" Dimensionen haben. Der alte Tisch hat eine Breite von 1,50m und eine Tiefe von 80cm. Der neue wird 2m breit und 1m tief.
7. Hardtubing in den sichtbaren Bereichen und Softtubing (durch den ausfahrbaren Korpus bedingt) in den unsichtbaren.
8. Thema RGB-Beleuchtung: Natürlich wird so ein Projekt eine entsprechend umfangreiche RGB-Beleuchtung erhalten. Mir ist durchaus bewusst, dass sich daran die Geister scheiden. Das ist so wie das "Modern Talking Syndrom" früher... Keiner hat die Musik gehört wenn man gefragt hat und trotzdem waren die ständig auf Platz 1 und haben Millionen an Platten verkauft. RGB-Beleuchtung im PC-Markt hat den selben Effekt. In den Foren wird darüber nur gemeckert und gemotzt und trotzdem werden von den Herstellern immer mehr Komponenten und Peripherie-Geräte mit den kleinen bunten Lichtchen versehen. Und diese müssen sich ja anscheinend auch entsprechend gut verkaufen. Warum würden die Hersteller sonst immer mehr davon auf den Markt werfen.
Daher oute ich mich jetzt einmal selbst: Richtig eingesetzt finde ich RGB-Beleuchtung eigentlich richtig gut. Besonders wenn man beim zocken an einem heißen Sommertag tief in ein Game eingetaucht ist und Außentemperaturen von 36-40 Grad herrschen findet eine RGB-Beleuchtung die sich wegen überhöhter Systemtemperaturen kritisch rot verfärbt doch viel praktischer als ein kleines Temperaturdisplay das man im eifer des Gefechtes gerne mal aus den Augen verliert. Und für alle, die RGB-Beleuchtung nicht mögen: Man kann sie abschalten.
9. Auch dieses mal will ich soviel Peripherie/Geräte wie möglich (z.B. Soundbar, Subwoofer, usw.) in dem Tisch selbst integrieren.
10. Als besonderen Clou und Gimmick werde ich in das "Good & Evil"-Projekt noch zwei hochauflösende LED-Matrix-Displays im ausfahrbaren Korpus verbauen. Mit diesen Displays plane ich so einiges anzustellen. Auch über diese will ich z.B. Systeminformationen einblenden lassen, Newsfeeds/Newsticker laufen lassen, während dem Gamen zum Spiel passende Ambiente-Animationen ablaufen lassen, mich über eingehende eMails informieren, usw.
2. Zwei in den Korpus eingelassene Touchscreens, zur Anzeige von Systemdaten und zur Steuerung diverser Systemfunktionen. Diese übernehme ich ebenfalls aus dem Vorgängerprojekt. Allerdings werden sie diesmal wesentlich zugänglicher und sinnvoller verbaut.
3. Zusammenhängend mit den Touchscreens plane ich die Integration von einem oder zwei Raspberry-Pi's um über diese Sensordaten auszulesen, die Beleuchtung zu steuern und falls möglich noch ein paar andere Funktionen. Da ich mich allerdings noch nie so intensiv mit dem Pi beschäftigt habe, werde ich mich in die Thematik noch ein wenig herein arbeiten müssen.
4. Die Monitore werden in einem Korpus sitzen, der sich ein- und ausfahren lässt.
5. Der Haupt-Spiel-Monitor wird ein selbstgebautes Ambilight-ähnliches System zur Umgebungsbeleuchtung erhalten um die Immersion bei Spielen zu verstärken.
6. Das Projekt wird im Vergleich zu meinem alten Tisch recht "sportliche" Dimensionen haben. Der alte Tisch hat eine Breite von 1,50m und eine Tiefe von 80cm. Der neue wird 2m breit und 1m tief.
7. Hardtubing in den sichtbaren Bereichen und Softtubing (durch den ausfahrbaren Korpus bedingt) in den unsichtbaren.
8. Thema RGB-Beleuchtung: Natürlich wird so ein Projekt eine entsprechend umfangreiche RGB-Beleuchtung erhalten. Mir ist durchaus bewusst, dass sich daran die Geister scheiden. Das ist so wie das "Modern Talking Syndrom" früher... Keiner hat die Musik gehört wenn man gefragt hat und trotzdem waren die ständig auf Platz 1 und haben Millionen an Platten verkauft. RGB-Beleuchtung im PC-Markt hat den selben Effekt. In den Foren wird darüber nur gemeckert und gemotzt und trotzdem werden von den Herstellern immer mehr Komponenten und Peripherie-Geräte mit den kleinen bunten Lichtchen versehen. Und diese müssen sich ja anscheinend auch entsprechend gut verkaufen. Warum würden die Hersteller sonst immer mehr davon auf den Markt werfen.
Daher oute ich mich jetzt einmal selbst: Richtig eingesetzt finde ich RGB-Beleuchtung eigentlich richtig gut. Besonders wenn man beim zocken an einem heißen Sommertag tief in ein Game eingetaucht ist und Außentemperaturen von 36-40 Grad herrschen findet eine RGB-Beleuchtung die sich wegen überhöhter Systemtemperaturen kritisch rot verfärbt doch viel praktischer als ein kleines Temperaturdisplay das man im eifer des Gefechtes gerne mal aus den Augen verliert. Und für alle, die RGB-Beleuchtung nicht mögen: Man kann sie abschalten.
9. Auch dieses mal will ich soviel Peripherie/Geräte wie möglich (z.B. Soundbar, Subwoofer, usw.) in dem Tisch selbst integrieren.
10. Als besonderen Clou und Gimmick werde ich in das "Good & Evil"-Projekt noch zwei hochauflösende LED-Matrix-Displays im ausfahrbaren Korpus verbauen. Mit diesen Displays plane ich so einiges anzustellen. Auch über diese will ich z.B. Systeminformationen einblenden lassen, Newsfeeds/Newsticker laufen lassen, während dem Gamen zum Spiel passende Ambiente-Animationen ablaufen lassen, mich über eingehende eMails informieren, usw.
Das Design:
Stellt sich natürlich noch die Frage, wie der neue Tisch denn nun aussehen soll. Wie auch schon in der Vergangenheit habe ich das neue Projekt mit SketchUp grob entworfen und dann mit Raylectron und Blender entsprechend gerendert. Beim Bau werde ich mich auch diesmal weitestgehend an meinen Entwürfen orientieren. Es gibt aber auch noch Bereiche, die sich während der Umsetzung noch ändern können/werden.
Doch jetzt erst einmal genug geschwafelt: Hier präsentiere ich mein Vorabentwürfe, die ich dann bei Bedarf noch anpassen werde:
Materialien:
Im Gegensatz zum vorherigen Projekt werde ich diesmal mit MDF-Platten als Hauptbaumaterial arbeiten. MDF ist wesentlich stabiler und "steifer" als die beim letzten mal verwendeten Möbelbauplatten. Dies ist gerade für den ausfahrbaren Korpus sehr wichtig. Allerdings kommt mit den MDF-Platten auch ein höheres Gewicht daher, was dem Hebemechanismus hoffentlich nicht zu sehr zu schaffen machen wird. Hinzu kommen dann noch Plexiglas und echtes Glas und das ein oder andere Teil aus dem 3D-Drucker.
Sponsoring:
Diejenigen unter Euch, die schon mein letztes Projekt verfolgt haben können sich vielleicht daran erinnern, dass ich das "Heaven & Hell" Projekt damals ohne einen Sponsor und Unterstützung begonnen hatte. Nachdem damals aber ein Unternehmen hier im Forum auf das Projekt aufmerksam wurde und mir ein wenig Unterstützung zur Seite stellte. Im Laufe des Projektes kamen dann noch ein paar hinzu und haben es mir ermöglicht mein Budget auf den eigentlichen Bau zu verwenden.
Auch bei diesem Projekt werde ich meinen selbst gesetzten Kostenrahmen locker und schneller sprengen als mir lieb sein dürfte, daher habe ich mich diesmal dazu entschieden schon im Vorfeld nach entsprechender Unterstützung zu suchen und bin auch entsprechend fündig geworden.
Daher möchte ich mich schon jetzt bei den folgenden Unternehmen für ihre Unterstützung und den Support meines Projektes bedanken: (in alphabetischer Reihenfolge)
Alphacool
Für die Versorgung mit Kühlkomponenten und Zubehör.
Cooler Master
Für Lüfter, Netzteil, Tastatur, Maus, Mauspad
Flatlift TV Liftsysteme GmbH
Für das zur Verfügung stellen eines geeigneten Hebesystems für den ausfahrbaren Korpus
MSI Deutschland
Für die Versorgung mit entsprechenden Systemkomponenten
XPG/AData
Für die Grundausstattung mit RAM-Kits und SSDs.
Tausend Dank dafür !!!
Farbgebung:
Ich habe mich noch nicht endgültig auf eine Farbe für den Tisch festgelegt. Mit dem entsprechenden Arbeitsaufwand lassen sich die MDF-Platten aber in jeder Farbe lackieren. Auch bin ich mir noch nicht schlüssig ob der Tisch am Ende ein Hochglanz- oder ein mattes Finish erhalten wird. Eventuell wird das Projekt auch mehrfarbig (Hauptfarbe / Akzentfarbe).
Um mal einen Eindruck vom möglichen Endergebnis zu bekommen, habe ich mal ein wenig mit den virtuellen Farbeimern von Blender rumgespielt. Hier die Ergebnisse:
Mal schauen was es dann im Endeffekt werden wird....
Der Anfang:
Anfangen werde ich morgen mit dem zusägen der MDF-Platten und dann in den folgenden Tagen mit dem hinteren Teil des Korpus und mit dem ausfahrbaren Bereich.
Meine Erwartungen an diesen Thread und die Community:
Bei dem letzten Tisch-Projekt hat mich am meisten der Support und der Input aus der Community gefreut. Das ein oder andere von Euren Ideen hat es ja dann schließlich auch mit in das Projekt geschafft. Von daher würde ich mich auch diesmal über jede Menge "konstruktiven" Input und entsprechende Hilfestellungen bei eventuell auftauchenden Problemen freuen. Vielleicht verirrt sich ja auch der ein oder andere Abonnent vom letzten Projekt hierher...
Auch erhoffe ich mir ähnlich viel Spaß bei der Umsetzung wie beim letzten mal und vielleicht entstehen ja auch wieder neue Forenfreundschaften (von der es manche beim letzten Mal auch ins Real-Life geschafft haben).
Ich hoffe Ihr habt an diesem Worklog ähnlich viel Spaß, wie auch ich ihn haben werde.
So, zum Abschluss habe ich auch schon wie beim letzten mal ein Rendervideo erstellt, dass den grundsätzlichen Projektaufbau im Detail zeigt. Auf dem gleichen YT-Kanal werde ich nach Möglichkeit von Zeit zu Zeit das ein oder andere Video einstellen um bestimmte Details näher zu beleuchten.
Datenschutzhinweis für Youtube
An dieser Stelle möchten wir Ihnen ein Youtube-Video zeigen. Ihre Daten zu schützen, liegt uns aber am Herzen: Youtube setzt durch das Einbinden und Abspielen Cookies auf ihrem Rechner, mit welchen sie eventuell getracked werden können. Wenn Sie dies zulassen möchten, klicken Sie einfach auf den Play-Button. Das Video wird anschließend geladen und danach abgespielt.
Youtube Videos ab jetzt direkt anzeigen
Und nun wünsche ich Euch und mir viel Spaß mit meinem "Good & Evil" Projekt.
Viele Grüße,
Olli, aka Quantor
Zuletzt bearbeitet: